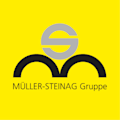
Text von Redaktion
veröffentlicht 21.12.2021
aktualisiert 29.05.2024
veröffentlicht 21. Dezember 2021
| aktualisiert 29. Mai 2024
6 min. Lesezeit
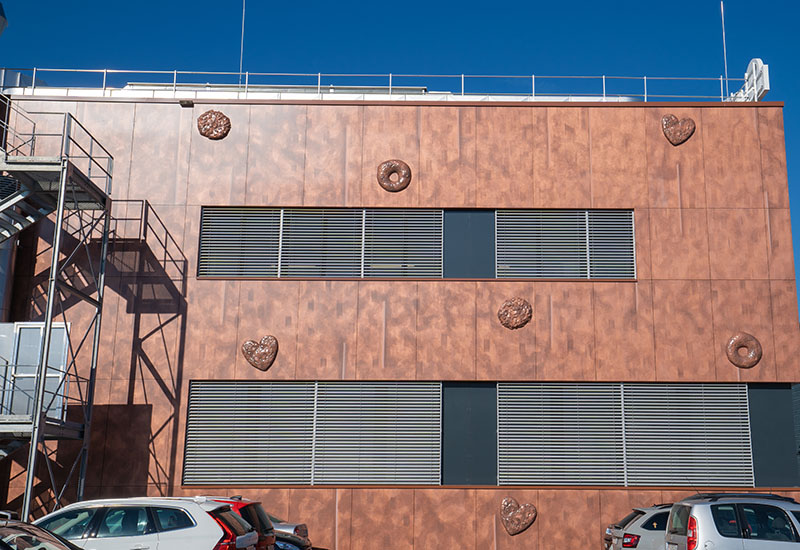
DAR-VIDA oder Choco Petit Beurre werden schon länger in Malters produziert. Ab diesem Jahr werden auch alle anderen Spezialitäten der Wernli AG hier hergestellt. Zwar gehört Wernli seit 2008 zu Hug, hat aber bis heute an seinem Hauptsitz in Trimbach produziert. Mit dem Generationenprojekt Backhaus Malters konzentriert die Hug AG ihre Infrastruktur. «Insgesamt investieren wir 60 Millionen Franken, das entspricht einem Halbjahresumsatz», sagt Andreas Hug, Co-Geschäftsleiter der Hug AG. 95 Prozent dieser Summe werde in der Schweiz investiert. «Der Standort Schweiz ist für uns ausgesprochen wichtig. So weit als nur möglich berücksichtigen wir Unternehmer aus der Region oder noch lieber aus dem Ort», bestätigt Hug. Bislang waren in Malters vier Produktionslinien in Betrieb. Mit dem Neubau erhöht sich diese Zahl auf neun; die Produktionsfläche wächst von 12 000 auf 22 000 Quadratmeter. Teil des Projekts ist zudem ein automatisiertes Lagerhaus mit tausend Palettenplätzen. Durch die zentrale Lagerhaltung können Aussenstandorte aufgegeben und Lastwagenfahrten verringert werden.
Trotz seiner Grösse sei das Bauvorhaben auf Kurs, weiss Fritz Steiner, Leiter Technik/Immobilien bei der Hug AG. «Im Frühling gab es gewisse Verzögerungen wegen der Coronamassnahmen. Doch dank guter Planer und Unternehmer, die miteinander alle den ‹Rank› finden, konnten wir den Rückstand aber wieder aufholen.» Ein wichtiger Grund für den reibungslosen Ablauf sei die vorgängige, sehr sorgfältige Planung. Man habe viel Zeit investiert, um eine gute Lösung zu finden, was sich nun auszahle.
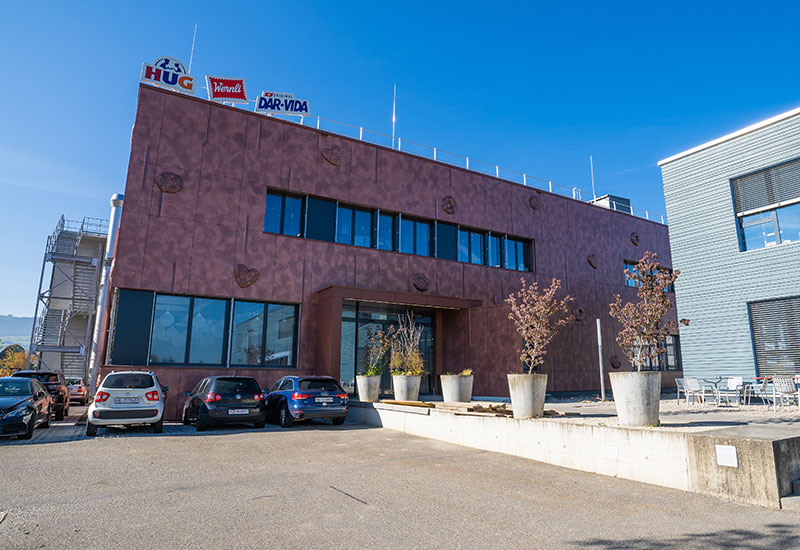
Objekt: Backhaus HUG Malters
Bauherr: HUG AG, Malters
Planer: Cerutti Partner Architekten AG
Bauunternehmung: Anliker Bauunternehmung, Emmenbrücke
Vorfabrizierte Betonelemente: MÜLLER-STEINAG ELEMENT AG, Werk Schachen
Baujahr: 2019/2021
Betonelementbau aus guten Gründen
Schon beim bestehenden Ursprungsbau 1967/68 wurde die Ausführung in Beton-Skelettbauweise gewählt, nachdem verschiedene moderne Produktionsbetriebe in mehreren europäischen Ländern besichtigt worden waren. Die wichtigsten Argumente für den Elementbau waren die möglichen grossen Spannweiten, das heisst stützenfreie Halle und Hygiene aufgrund wenig horizontaler Flächen.
Für die Erweiterung wurde die Konstruktionsweise nochmals offen angegangen. Der Entscheid war schnell klar: Man wollte beim Betonelementbau bleiben. Die Argumente von 1967 gelten heute genauso wie damals, womit die Wahl des Konstruktionssystems naheliegend schien. Ein Systemwechsel für die Erweiterung hätte kaum Vorteile gebracht, eine Übernahme der Geschossniveaus und der Spannweiten wäre nicht möglich gewesen. So liessen sich vom Bestand die geometrischen Gegebenheiten für den Anbau und die Aufstockung übernehmen; mit den Rippenplatten konnte entsprechend Gewicht gespart werden. Ferner gelang es, eine minimale Rippenhöhe für eine maximale Raumhöhe zu erreichen und die statischen Anforderungen wie auch eine Erdbebenstabilisierung zu erfüllen. «Die Elementgeometrie wurde zwischen Architekt und Bauingenieur definiert. Danach wurde die MÜLLER-STEINAG ELEMENT AG einbezogen, die die Elemente hergestellt, geliefert und montiert hat», dokumentiert Ingenieur Luciano Lötscher von der Basler & Hofmann AG die Abläufe.
Synergien zu nutzen war somit nicht nur das Kredo bei der strategischen Ausrichtung der Firma Hug, sondern wurde auch in der Konzipierung des neuen Backhauses umgesetzt – unter Anwendung modernster bauplanerischer und -kommunikativer Vernetzungsstandards wie BIM (Building Information Modeling). Vorteile wurden auch in der kurzen Aufrichtzeit gesehen: Durch das Bauen mit Elementen liess sich der Betonierprozess auslagern und die aufgelöste Fassade des bestehenden Baus in minimaler Zeit wieder schliessen, womit der Backbetrieb trotz Um- und Anbauarbeiten stets aufrechterhalten bleiben konnte. Dies erforderte eine planerische Maximalleistung für das zeitgenaue Produzieren, Lagern, Liefern, Zwischenlagern und Montieren der verschiedenen Betonelementtypen. Innerhalb des Skelettsystems wurde einzig der Überbeton, der die Elemente stabilisiert und die Querkräfte an die dafür vorgesehenen aussteifenden Ortbetonscheiben überträgt, vor Ort betoniert. Gleichzeitig übernahm der Überbeton auch die Funktion des Bodens der jeweiligen Produktionsabschnitte. Die vorgesehene Nutzlast wurde dabei in der Vorspannung der Rippendeckenelemente berücksichtigt.
Betonelemente
115 Stück ELEF® Fassadenelemente
230 Stück ELEF® Stützen
300 Stück ELEF® Rippenplatten
140 Stück ELEF® Hutträger
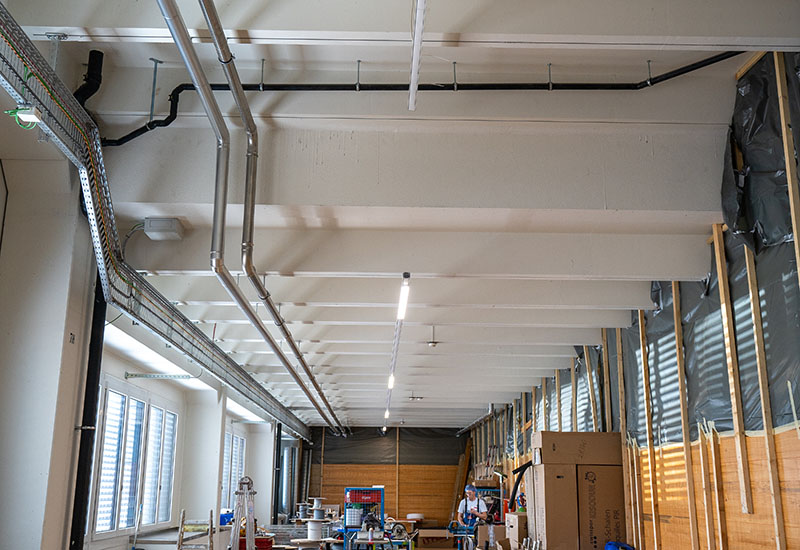
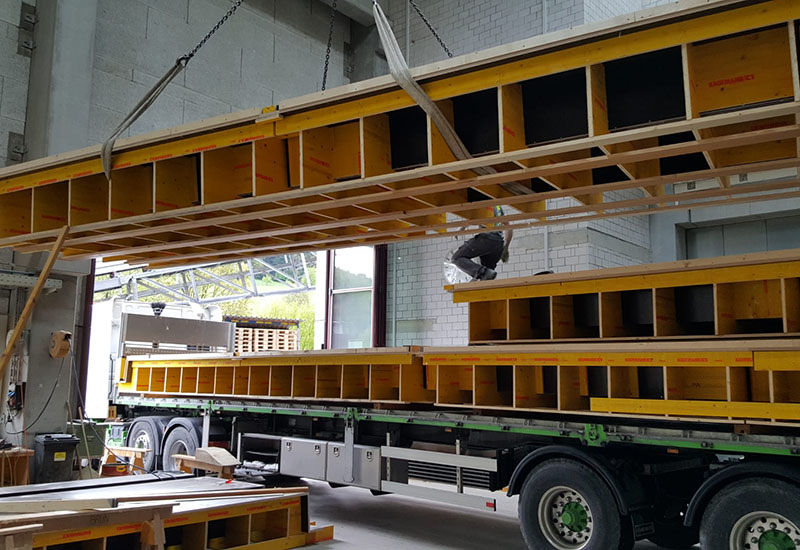
Dienstleistungen
Gruppeninterner Schalungsbau
Werkseitige Vorfabrikation der einzelnen Elemente
Werkseitige Vorspannung
Just-in-time-Lieferungen der Betonelemente auf die Baustelle
Montage aller Betonelemente
Verwendung von Betonelementen aus ökologischen Überlegungen
Die Bauherrschaft ist sehr darauf bedacht, den ökologischen Fussabdruck des neuen Gebäudes möglichst klein zu halten. Das Elementwerk in Schachen, nur fünf Autominuten von der Baustelle entfernt, erweist sich für dieses Ansinnen als ideal. «Im Auftrag der Firma Anliker AG war die MÜLLER-STEINAG ELEMENT AG mit ihrem nahegelegenen Werk als zuverlässige und innovative Partnerin zur Umsetzung dieses Projekts wie prädestiniert», bestätigt Bau- und Projektleiter Samuel Amrein vom Planungsbüro Cerutti Partner. Eine besondere Herausforderung stellten in diesem Zusammenhang die Fassadenelemente dar. Aus ökologischen Gründen wollte man die zurückgebauten Elemente der aufgelösten Fassade nicht einfach rezyklieren, sondern an der neuen Fassade wiederum als raumabschliessende Elemente übernehmen. Insofern gaben die alten Elementformen und Abmessungen auch die Einteilung und Gestaltung des neuen Fassadenbildes vor. Die Herausforderung betraf dabei vor allem die ausführenden Firmen MÜLLER-STEINAG ELEMENT AG und Anliker, die die bestehenden Elemente möglichst verlustfrei sichern, demontieren, sortieren, zwischenlagern und wiederum neu montieren mussten. Was hier einfach klingt, stellte sich auf der Baustelle teilweise als Knacknuss heraus. Die bestehenden Elemente stammten aus zwei Bauzeiten aus den 60er und 80er Jahren. Die Sandwichkonstruktionen der alten Elemente waren teils nur durch dünne Armierungshaken miteinander verbunden und mussten mittels Kernbohrungen und Kranhaken doppelt gesichert werden. Hinzu kommt, dass einige der dafür vorgesehenen Gewinde der Lasthaken für die Kranarbeiten nicht mehr den heutigen Normen und Grössen entsprachen. Dazu mussten eigens neue Kranhaken angefertigt werden.
Spektakuläre Aufrichtarbeiten
Überhaupt mussten für das Backhaus sehr viele und verschiedene Elementtypen in mehreren unterschiedlichen Etappen im Werk hergestellt, auf die Baustelle geliefert und am Objekt montiert werden. «In welcher Reihenfolge sie produziert und gelagert wurden, damit der Verlad, die Lieferung und die Montage reibungslos funktionierten, stellte eine erhebliche planerische und logistische Herausforderung dar. Alles musste unter Berücksichtigung örtlich enger Platzverhältnisse und erschwerter Zugänglichkeiten punktgenau und just-in-time funktionieren», berichtet Objektleiter Martin Bölk vom Werk Schachen MSE. Es ist die schiere Menge verschiedenster Fassadenelemente (115 Stück), Stützen (230 Stück), Rippenplatten (300 Stück) und Hutträger (140 Stück) mit insgesamt nicht weniger als 6200 m3 Betonvolumen, die von der Werkplanung höchste Aufmerksamkeit und Sorgfalt abforderte.
«Die Aufrichtarbeiten waren sehr beeindruckend mitanzusehen», schwärmt Bauplaner und Architekt Samuel Amrein. «Die Montageequipen im Zusammenspiel mit Pneukran – dieser musste teils mittels Kamera und nur durch Anweisungen via Funk auf der gegenüberliegenden Seite seines Standorts arbeiten – leisteten Hochpräzisionsarbeit.» Ebenso viel Begeisterung löste die Besichtigung des nahe gelegenen Betonelement-Werks im Beisein der Bauherrschaft aus, wo man die für die Baustelle vorgesehenen Teile bei deren Herstellung beobachten und anschauen konnte. Mit den Firmen MÜLLER-STEINAG ELEMENT AG und Anliker waren kompetente Fachpartner an Board, die ihre langjährige Erfahrung im Sinn der Bauherrschaft einsetzten und alle Herausforderungen mit Geschick und gut vernetztem Denken angingen und eine für alle zufriedenstellende Lösung vorlegen konnten.
«Via Planer und aus den wenigen Direktkontakten haben wir mit der MÜLLER-STEINAG ELEMENT AG einen kompetenten und zuverlässigen Partner kennengelernt, mit dem wir durchaus wieder zusammenarbeiten würden, bestätigt Fritz Steiner im Namen der rundum zufriedenen Bauherrschaft.
Überzeugen auch Sie sich von den Dienstleistungen der MÜLLER-STEINAG ELEMENT AG oder nehmen Sie direkt Kontakt mit uns auf, wir beraten Sie gerne.