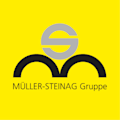
Texte de Redaktion
publié 21.12.2021
mis à jour 11.03.2024
publié 21. décembre 2021
| mis à jour 11. mars 2024
8 min. Temps de lecture
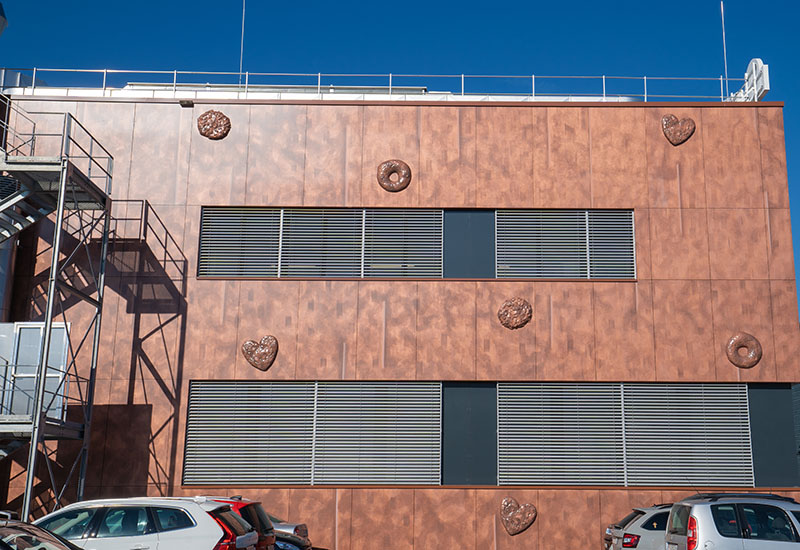
DAR-VIDA ou Choco Petit Beurre sont produits depuis longtemps à Malters. A compter de cette année, toutes les autres spécialités de la société Wernli AG seront également fabriquées ici. Wernli a beau appartenir à Hug depuis 2008, elle a produit jusqu’à aujourd’hui sur le site de son siège principal à Trimbach. Avec le projet intergénérationnel du fournil de Malters, la société Hug AG concentre son infrastructure. «Au total, nous investissons 60 millions de francs, ce qui correspond à un chiffre d’affaires d’un semestre», explique Andreas Hug, co-directeur de Hug AG. 95% de cette somme seront investis en Suisse. «Le site suisse compte beaucoup pour nous. Dans la mesure du possible, nous tenons compte des entrepreneurs régionaux, voire, mieux encore, locaux», confirme Andreas Hug. Jusqu’à présent, quatre lignes de production étaient en service à Malters. Avec le nouveau bâtiment, ce nombre passe à neuf; la surface de production passe de 12 000 à 22 000 mètres carrés. Un entrepôt automatisé d’un millier de palettes s’inscrit également dans le projet. Le stockage centralisé permet d’abandonner les sites extérieurs et de réduire les trajets en camion.
Malgré son envergure, le projet de construction est sur la bonne voie, assure Fritz Steiner, responsable Technique/Immobilier de Hug AG. «Au printemps, il y a eu quelques retards à cause des mesures liées à la pandémie. Mais grâce à de bons planificateurs et entrepreneurs, qui savent se montrer dégourdis, nous avons pu rattraper notre retard.» L’une des principales raisons du bon déroulement découle d’une planification très minutieuse en amont. On a investi beaucoup de temps pour trouver une bonne solution, ce qui porte aujourd’hui ses fruits.
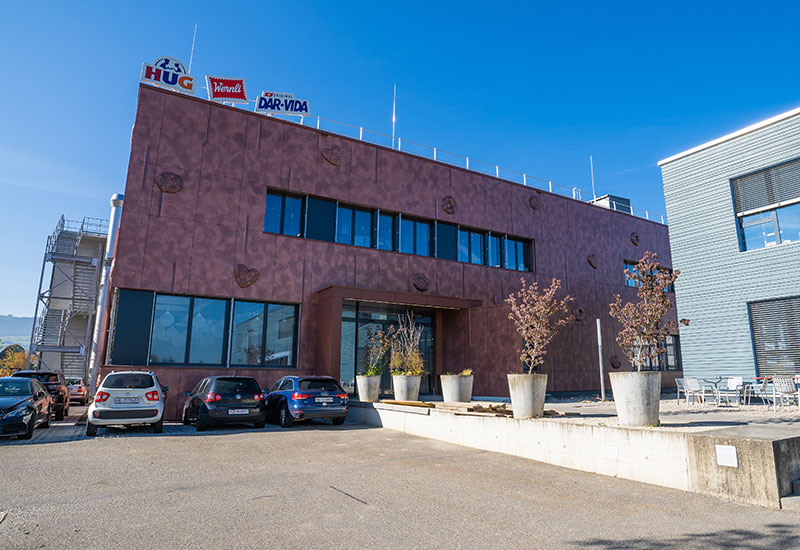
Objet: Le fournil Hug de Malters
Maître d’ouvrage: HUG AG, Malters
Planificateur: Cerutti Partner Architectes AG
Entreprise de construction: Entreprise de construction Anliker, Emmenbrücke
Eléments en béton préfabriqués: MÜLLER-STEINAG ELEMENT AG, usine de Schachen
Année de construction: 2019/2021
La construction d’éléments en béton pour de bonnes raisons
Déjà en 1967/68 pour la construction d’origine existante, on avait opté pour la réalisation d’une ossature en béton après avoir visité différentes entreprises de production modernes dans plusieurs pays européens. Les principaux arguments en faveur de la construction par éléments étaient les portées importantes possibles, c’est-à-dire un hall sans appui, et l’hygiène en raison du peu de surfaces horizontales.
Pour l’extension, le mode de construction a été à nouveau abordé de manière ouverte. La décision ne s’est pas fait attendre: rester sur une construction d’éléments en béton. Les arguments de 1967 sont tout aussi valables aujourd’hui qu’à l’époque, le choix du système de construction était donc évident. Un changement de système pour l’extension n’aurait apporté que peu d’avantages, une reprise des étages et des portées n’aurait pas été possible. Ainsi, les données géométriques existantes ont pu être reprises pour l’extension et la surélévation; les plaques à nervures ont permis une économie du poids correspondant. En outre, il a été possible d’obtenir une hauteur de nervure minimale pour une hauteur de pièce maximale et de répondre aux exigences statiques ainsi que d’obtenir une stabilisation sismique. «La géométrie des éléments a été définie entre l’architecte et l’ingénieur civil. Ensuite, nous avons fait appel à MÜLLER-STEINAG ELEMENT AG, qui a fabriqué, livré et monté les éléments», étaye l’ingénieur Luciano Lötscher de Basler & Hofmann AG.
L’utilisation de synergies n’était donc pas seulement le credo de l’orientation stratégique de l’entreprise Hug: elle a aussi été mise en œuvre dans la conception du nouveau fournil en utilisant les normes de mise en réseau les plus modernes en matière de planification et de communication dans le domaine de la construction, comme le BIM (Building Information Modeling). Des avantages se sont aussi profilés dans le temps de construction rapide: la construction par éléments a permis de délocaliser le processus de bétonnage et de refermer en un minimum de temps la façade disloquée du bâtiment existant, permettant ainsi de poursuivre les activités de fournil malgré les travaux de transformation et d’extension. Une planification maximale a été nécessaire pour produire, stocker, livrer, entreposer et monter les différents types d’éléments en béton en temps voulu. Au sein du système d’ossature, seule la surépaisseur, qui stabilise les éléments et transmet les forces transversales aux plaques consolidantes de béton prévus à cet effet, a été coulée sur place. Parallèlement, la surépaisseur est utilisée comme sol pour les sections de production respectives. La charge utile prévue a ainsi été prise en compte dans la précontrainte des éléments de plafond à nervures.
Éléments en béton
115 pièces éléments de façade ELEF®
230 pièces poteaux ELEF®
300 pièces plaques à nervures ELEF®
140 pièces poutres principales ELEF®
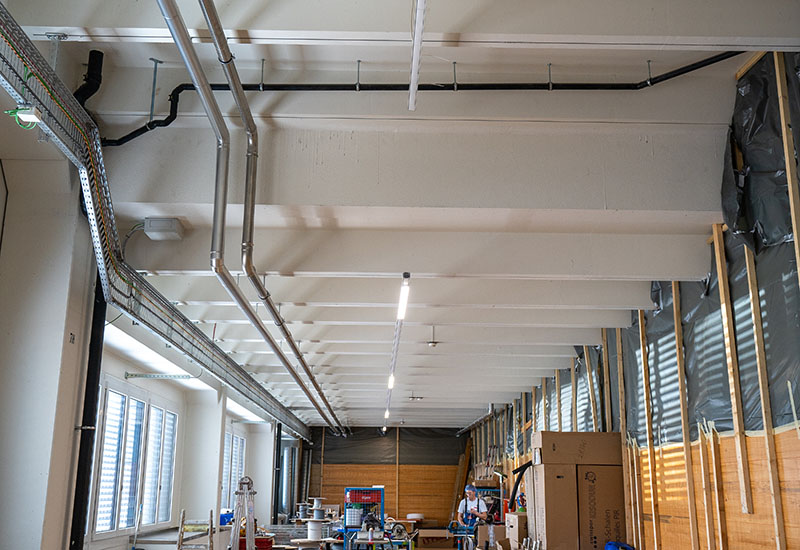
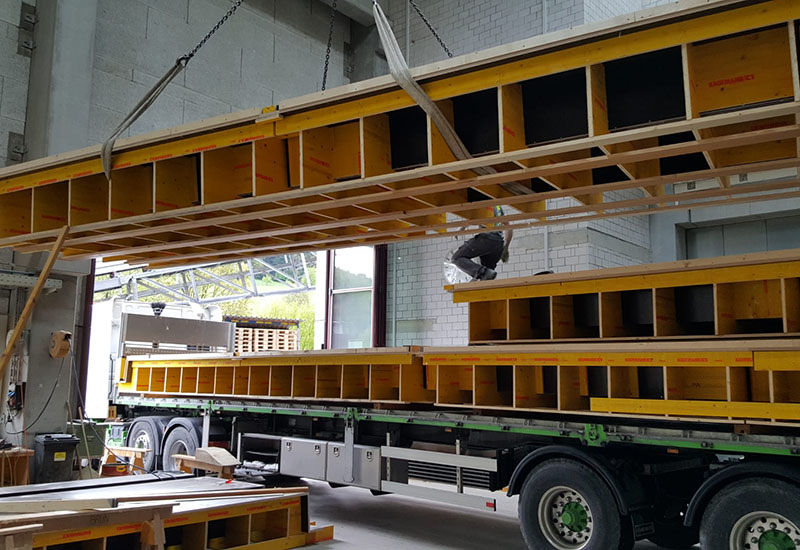
Prestations
Construction de coffrage interne au groupe
Préfabrication en usine des différents éléments
Précontrainte en usine
Livraisons just-in-time des éléments en béton sur le chantier
Montage de tous les éléments en béton
Utilisation d’éléments en béton pour des raisons écologiques
Le maître d’ouvrage est très soucieux de réduire au maximum l’empreinte écologique du nouveau bâtiment. L’usine d’éléments de Schachen, située à cinq minutes en voiture du chantier, s’avère idéale dans cette perspective. «Mandatée par l’entreprise Anliker AG, MÜLLER-STEINAG ELEMENT AG, avec son usine proche, s’est imposée pour la réalisation de ce projet en tant que partenaire de confiance et innovant», confirme le chef de chantier et de projet Samuel Amrein du bureau d’études Cerutti Partner. Dans ce contexte, les éléments de façade constituaient un défi particulier. Pour des raisons écologiques, la volonté n’était pas de recycler les éléments démontés de la façade supprimée, mais de les reprendre sur la nouvelle façade pour en faire des éléments qui délimitent de l’espace. De fait, les anciennes formes et dimensions des éléments ont également dicté la répartition et la conception du nouvel aménagement de la façade. Le défi concernait surtout les entreprises exécutantes MÜLLER-STEINAG ELEMENT AG et Anliker, qui devaient sécuriser, démonter, trier, stocker temporairement et remonter les éléments existants avec le moins de pertes possible. Ce qui semble simple sur le papier s’est parfois révélé être un casse-tête sur le chantier. Les éléments existants dataient de deux périodes de construction, des années 1960 et 1980. Les constructions en sandwich des anciens éléments n’étaient en partie reliées entre elles que par de fins crochets d’armature et devaient être doublement sécurisées au moyen de carottages et de crochets de grue. Par ailleurs, certains des filetages des crochets de levage prévus à cet effet pour les travaux de grutage ne correspondaient plus ni aux normes ni aux tailles actuelles. Il a donc fallu fabriquer de nouveaux crochets de grue.
Des Travaux d’élévation spectaculaires
De nombreux types d’éléments différents ont dû être fabriqués en usine en plusieurs étapes, puis livrés sur le chantier pour être montés sur le bâtiment. «L’ordre dans lequel ils ont été produits et stockés, afin que le chargement, la livraison et le montage se déroulent sans problème, a représenté un défi considérable en termes de planification et de logistique. Tout devait fonctionner avec précision et just-in-time, compte tenu du manque d’espace et des difficultés d’accès», rapporte le responsable de projet Martin Bölk de l’usine Schachen MSE. La planification de l’ouvrage a dû faire preuve d’une attention et d’un soin extrêmes en raison de la quantité d’éléments de façade (115 pièces), de poteaux (230 pièces), de plaques à nervures (300 pièces) et de poutres principales (140 pièces), soit pas moins de 6200 m3 de béton.
«Les travaux d’élévation étaient très impressionnants», s’enthousiasme Samuel Amrein, planificateur de construction et architecte. «Les équipes de montage et la grue sur pneus, qui devait travailler en partie à l’aide d’une caméra et uniquement en suivant des instructions par radio du côté opposé où elle se tenait, ont fourni un travail de haute précision.» La visite de l’usine d’éléments en béton toute proche, en présence du maître d’ouvrage, a suscité tout autant d’enthousiasme, puisqu’il a été possible d’y observer et d’y voir les éléments prévus pour le chantier au fil de leur fabrication. Les entreprises MÜLLER-STEINAG ELEMENT AG et Anliker se sont révélées des partenaires compétents qui ont mis leur longue expérience au service du maître d’ouvrage et qui ont relevé tous les défis avec brio et une bonne réflexion en accord pour présenter une solution satisfaisante pour tous.
«Par l’intermédiaire du planificateur et des quelques contacts directs, nous avons fait la connaissance de MÜLLER-STEINAG ELEMENT AG, un partenaire fiable et compétent avec lequel nous pourrions à nouveau travailler, confirme Fritz Steiner au nom du maître d’ouvrage entièrement satisfait.
Laissez-vous convaincre par les services de MÜLLER-STEINAG ELEMENT AG ou contactez-nous directement, nous vous conseillerons avec plaisir.