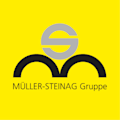
Text von Redaktion
veröffentlicht 04.05.2018
aktualisiert 06.06.2025
veröffentlicht 04. Mai 2018
| aktualisiert 06. Juni 2025
4 min. Lesezeit

Das Objekt
Im Rahmen der Arealentwicklung der F. HOFFMANN-LA ROCHE AG sollte auf den Baufeldern C3 und C4 ein neues Parkhaus «Bau 253» für ca. 2000 Parkplätze erstellt werden. Durch den Rückbau des alten, bestehenden Parkhauses «Bau 226» sowie weiterer Aussenparkplätze konnte so Platz für die umfangreichen Erweiterungsbauten (Porten-, Service- und Bürogebäude) geschaffen werden. Um diese Nutzungsbauwerke schnellst möglich umsetzen zu können, wurde das Parkhaus in 2 Etappen dem Baubewilligungsverfahren zugeführt. Etappe 1 beinhaltete ca. 2/3 aller geforderten Parkplätze und Etappe 2 die verbleibenden Parkplätze bis zur Gesamtzahl von 2000.
Da die beiden Baugesuche nur wenige Monate auseinander lagen, wurde eine lückenlose Umsetzung von der 1. Etappe im Übergang zur 2. Etappe angestrebt.
Der heutige Parkhausneubau mit einer Grundfläche von 168,5 x 33 m besticht, wie das damalige Projekt, durch seine ausserordentlichen Dimensionen. Mit zwei Untergeschossen, dem Erdgeschoss und sechs Obergeschossen mit zusätzlichen Rückkühlereinheiten auf dem Dachgeschoss erreicht das Parkhaus eine Gesamthöhe von ca. 30,7 m resp. 25 m ab Terrain.
Die zur A3 in Längsrichtung angeordnete Lage minimiert zudem die Lärmimmissionen der Autobahn auf die künftigen Erweiterungsbauten auf ein Minimum. Gleichzeitig wurde auf dieser nach Süden ausgerichteten Autobahnseite an der Fassade geschossweise eine Photovoltaikanlage platziert. Die verbleibenden Aussenfassaden wurden mittels einer Lochblechfassade vollständig eingekleidet, was seinerseits Lärmimmissionen aus der Parkhausnutzung stark reduzieren konnte.
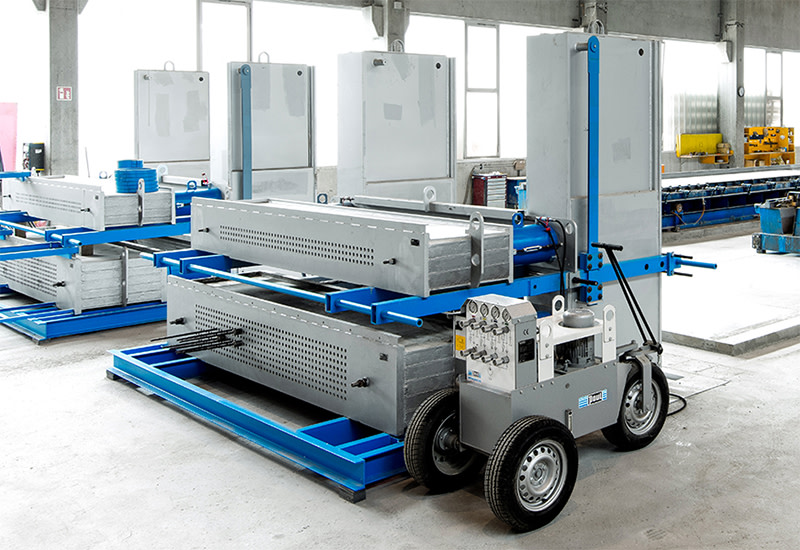
Systemparkhaus nach SIA und VSS
Die MÜLLER-STEINAG ELEMENT AG hat für Parkhäuser ein eigens sehr flexibles System nach den Vorgaben der SIA und VSS entwickelt. Das System eignet sich speziell für Grossprojekte wie jenes der Roche, aber auch für kleinere Projekte, und ermöglicht sehr kurze Realisierungszeiten.
Die Fahrbahn- und Parkierungsflächen bestehen aus vorgespannten Parkingplatten mit eigens entwickelten, deckenunterseitigen Kupplungen und einem verstärkten, oberen Plattenspiegel, welcher nach Montage direkt der Nutzung zugeführt werden kann. Sofern der Kunde dies nicht speziell wünscht, werden kosten- und unterhaltsintensive Aufbauten wie Überbeton, Gussasphalt und OS-Beschichtungen überflüssig.
Die Rutschsicherheit, die Abriebbeständigkeit, der Chloridwiderstand und die nachweisliche Brandbeständigkeit können aufgrund der speziellen Betonrezeptur mittels Prüfzeugnissen nach geltenden Normen und Richtlinien nachgewiesen werden. Die vertikale Tragwerksstruktur besteht aus Stahlstützen, auf Wunsch mit Duplex-Beschichtung, oder auch aus Betonstützen.
Partnerschaftlich mit General- oder Bauunternehmer
Für kleine bis mittelgrosse Parkhäuser tritt die MÜLLER-STEINAG ELEMENT AG selbst als Generalunternehmer auf und sichert so dem Bauherrn eine lückenlose Bauausführung von A-Z. Leistungen wie Aushub, Baumeistertätigkeiten, Fassaden, Haustechnik, etc. sind dann nebst dem Tragwerk aus Betonelementen und Stahlbau Bestandteil unserer umfassenden Leistungen.
Im Falle des Parkhaus Roche wurde jedoch in Zusammenarbeit mit der Implenia Schweiz AG, Buildings Local, Geschäftsstelle Aarau eine partnerschaftliche Lösung umgesetzt. Dieser Weg erwies sich als der Richtige. Beim Parkhaus Roche verlangte der sehr hohe Anteil an anspruchsvollen Ortbetonabschnitten, wie die parallel geführten und gewundenen Rampenbauwerke sowie diverse Unterflurbauten, hohe Fachkompetenz und Ressourcen, wie z. B. im Bereich Ortbeton, Haustechnik und vielem mehr.
Hohe Betriebs- und Fahrsicherheit
Die konsequente Anlehnung an die geltenden Normen und Vorschriften zeigt sich in der konstruktiven Umsetzung. Der Bauherr kann eigenständig die Komfortstufe nach VSS wählen (Parkplatzbreiten, etc.). Sämtliche Park- und Fahrbahnflächen sind ohne Stützen und so hindernisfrei ausgelegt und unscheinbare Kleinigkeiten wie die Randbordüren zeigen dem Nutzer frühzeitig seine «Grenzen» auf. Wo erforderlich, wird diese Sicherheit ergänzt durch Personenschutzgitter in den Absturzbereichen und/oder Anpralleinrichtungen nach SIA mit einer Last von 60 kN.
Bemessung Tragwerk
Für die Bemessung der Tragwerksstruktur des Parkhauses zeichneten sich die Ingenieure der MÜLLER-STEINAG ELEMENT AG verantwortlich. Dabei galt es, nebst den inneren Lasteinflüssen wie jene der Nutzlast, etc. auch die äusseren Einwirkungen aus Wind und Erdbeben zu ermitteln. Diese Schnittkräfte wurden an der Schnittstelle des Ortbetons an den Bauherreningenieur zur weiteren Bearbeitung weitergereicht.
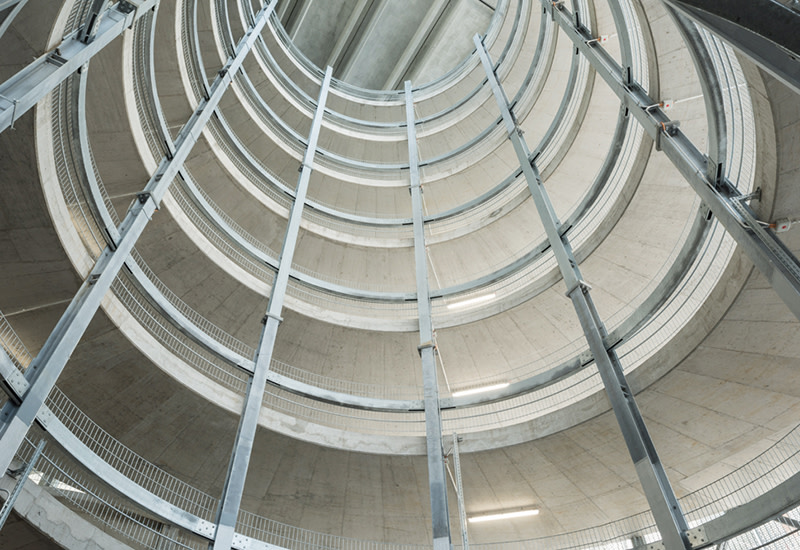
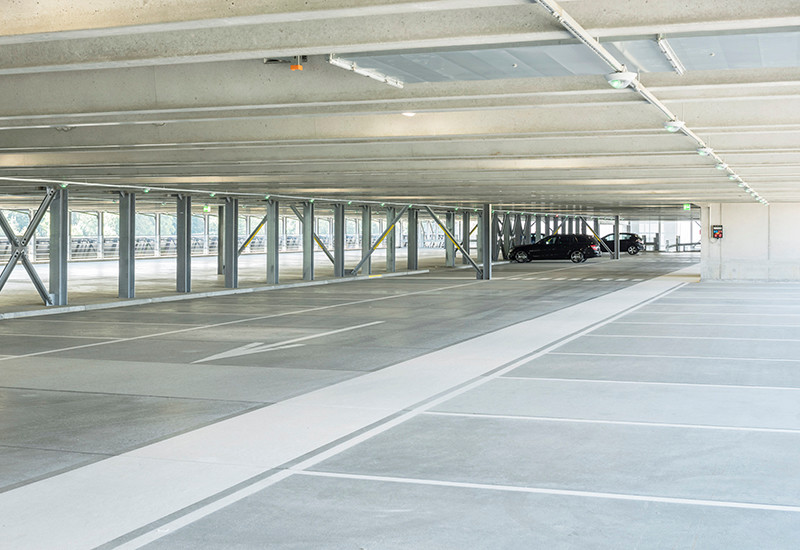
Hohe Verantwortung an die Masshaltigkeit
Das Parkhaus Roche benötigte insgesamt 1395 vorgespannte Parkingplatten und weitere Elemente sowie 525 to Stahlbau. Zur Sicherstellung reibungsloser Montageabläufe wurden alle Elemente im Werk der MÜLLER-STEINAG ELEMENT AG in einem eigens dafür erstellten Mockup im Massstab 1:1 unmittelbar nach der Produktion auf deren Masshaltigkeit geprüft. Die Auslieferung erfolgte dann Just-in-Time auf Abruf.
Fakten
Bauherr: F. Hoffmann-La Roche AG, Basel
Bauherrenplaner/-ingenieur: Jauslin Stebler, Rheinfelden (Ortbeton)
Auftraggeber: Implenia Schweiz AG, Buildings – Local, Aarau
Konzept Tragwerk Parkhaus: MÜLLER-STEINAG ELEMENT AG (Stahlbau und Elementbau), Schachen
Produktion und Montage Tragwerk: MÜLLER-STEINAG ELEMENT AG (Stahlbau und Elementbau), Schachen
Termine (Stahl- und Elementbau)
Beginn Ausführungsplanung: August 2014
Produktionsstart: Oktober 2014
Montage Etappe 1: März bis Mai 2015
Inbetriebnahme Etappe 1: Juni 2015
Montage Etappe 2: September bis November 2015
Inbetriebnahme Etappe 2: Frühjahr 2016